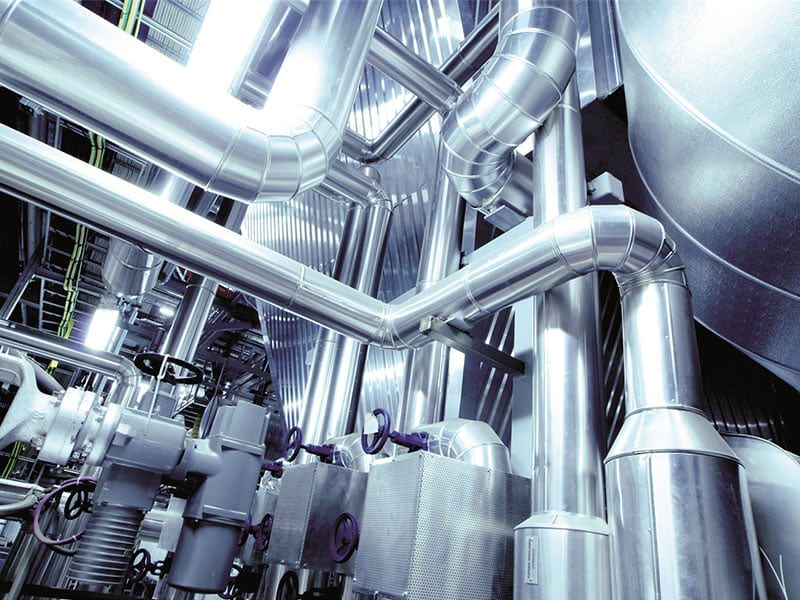
29 Mar Notes on assessment of equivalence of technical active substances
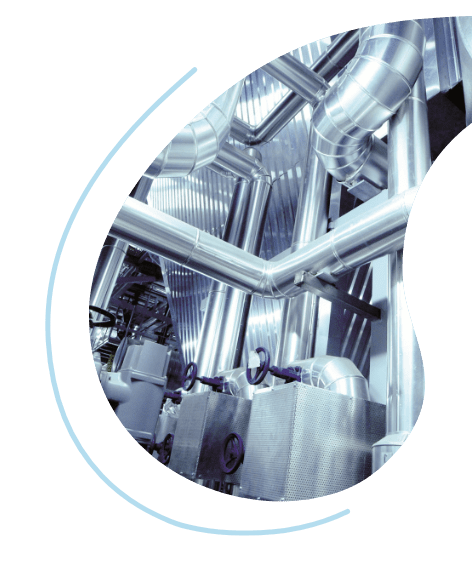
News
Notes on assessment of equivalence of technical active substances
On the first read, the Guidance Document on the Assessment of the Equivalence of Technical Materials of Substances regulated under Regulation (EC) No 1107/2009 (SANCO/10597/2003 –rev. 10.1 of 13 July 2012) does not seem complicated to an expert. However, applications for equivalence seldom result in an immediate approval. Often, the extra time and resources needed to address issues brought up by the competent authority could have be prevented.
Production sites and manufacturing processes for active substances for plant protection products need to be approved at EU level. In the active substance dossier the approved production location(s) and manufacturing processes are assessed and a reference specification is determined. This reference specification is part of the confidential part of the dossier and not available for third parties.
When companies wish to produce an active substance (or safener, or synergist) with a changed manufacturing process, and/or manufacturing location, then the ‘equivalence’ of this different source has to be assessed. This assessment should establish that the specification of the new source does not deviate significantly from the reference specification and that there is no increased toxicity compared to the reference source.
The assessment of equivalence is based on a 5-batch analysis and follows a two-tiered approach. Tier I consists of the evaluation of the identity of the active substance and impurities and the analytical methods used for the 5-batch analysis. If equivalence can be ascertained from these data, the Tier II assessment is not necessary. If equivalence cannot be established on the basis of the Tier I data, further mammalian toxicity/ecotoxicity consideration is necessary which will form the requirements of Tier II. If Tier II assessments cannot be addressed by QSARs and AMES-tests, adding a purification step in the production process is often considered the most effective way forward since it increases a successful Tier I assessment.
When filing an application for equivalence of a technical active substance in the EU, a report has to be submitted completed according to the guidance provided in the Guidance Document on the Assessment of the Equivalence of Technical Materials of Substances regulated under Regulation (EC) No 1107/2009 (SANCO/10597/2003 –rev. 10.1 of 13 July 2012). The key information submitted for the TIER I assessment consists of a report of an analysis of five batches of the technical active substance which determines the levels of the active substance and impurities >1 g/kg using validated methods. The competent authority will assess this data against the reference specification which in most cases is unknown to the applicant.
Only a small percentage of the applications were granted immediate approval. In nearly all cases the applicant was requested to address certain issues. Some of these issues concerned trivial matters such as the name and address of the supplier of the starting materials, the name of the person to contact at the manufacturing plant and his/her contact details, chromatograms of insufficient resolution, whether the batches analyzed were from full scale or from pilot production. However, in most cases more serious issues were identified during review, which were going to require much time and resources to address, and which could have been addressed relatively easily at an earlier stage during the performance of the studies that were submitted (five-batch analysis including method validation, screening studies), if only the focus on these issues had been right. A few of the most common issues identified during Tier 1 assessment of equivalence are discussed below.
The five-batch analysis is often preceded by a screening study which has the aim to identify which impurities could be present in the 5 batches with a specification equal to or exceeding 1 g/kg. Impurities which, based on the results of the screening study, are unlikely to occur in batches at levels >1 g/kg are not included in the analytical program of the five-batch analysis. Such a screening usually involves a combination of chromatographic techniques, such that all potential impurities, based on the production process, can be detected. The combination of techniques used should be adequate to detect all impurities potentially emanating from the production process. Sometimes applicants provide insufficient evidence that the chromatographic conditions used for screening are suitable for elution and separation of all potential impurities (e.g. isocratic elution instead of gradient elution). Sometimes the method used for screening is not suitable to detect certain potential impurities (e.g. certain starting materials), since they are not detectable using that method. For example, a starting material which does not absorb UV is not detectable using HPLC/UV, or HPLC/UV screening is performed at a wavelength which may not be most sensitive for certain postulated impurities, or for impurities of unknown structure.
Most production processes include the use of organic solvents. There must be experimental evidence that these solvents are not present at >1 g/kg in the batches. The presence of each solvent used in the production process and which could theoretically be present in the technical active substance is not always addressed in the screening study, and if necessary, in the five-batch analysis.
Frequently it was noted that the five batches used for the five-batch analysis were produced over a relatively short time period, and the conditions over this short time period (e.g. raw materials, technicians, equipment) may not be representative of the production process over a longer time span. If that is noted, either a new five-batch analysis is required, using batches spread over a sufficiently long period (6 months or more), or Quality Control (QC) data may be submitted of batches manufactured during the past years.
The validated LOQ for an impurity is sometimes above one or more of the levels of the impurity determined in the five batches. In that case a lower LOQ should be validated, confirming the validity of the measured levels of that impurity in the batches.
Applicants should provide an assessment of impurities that are not detected but that could theoretically be formed during the manufacturing process of the new source. These potential theoretical impurities should include process related impurities but also impurities of known toxicological concern. A list of impurities of known toxicological concern is provided in Appendix III of SANCO/10597/2003-rev. 10.1 of 13 July 2012). The potential occurrence of each of these impurities should be discussed. Many applications do not present an assessment of impurities of known toxicological concern. Particular attention should be given to the formation of N-nitroso-substituted compounds, which may occur in the presence of NOx during production processes that use or generate primary and secondary amines, where it is relevant to note that NOx could be formed from trace contamination (e.g. nitrites) that are present in the water used in the manufacturing process.
It is essential for agrochemical companies that the outsourcing laboratory of the five-batch analysis will take into account all these possible issues. This will be directly reflected in the execution of the equivalence assessment. Seeking regulatory advice at an early stage will prevent companies in incorrect decisions, gaps in the regulatory submission and will have an significant impact in the companies timeline and required resources.
Triskelion’s regulatory professionals will partner with you as an extension of your (regulatory) team and support you designing your 5 batch analytical program as if it were their own to make sure you get the data you need for your equivalence dossier. Our scientific advisors are ready to help you with efficient program design, navigating the regulatory requirements and mitigating risk, knowing your study will be done right. It is our goal to easy the process to market; lower risk or errors, eliminate inconsistencies and reduces the risk of delay.
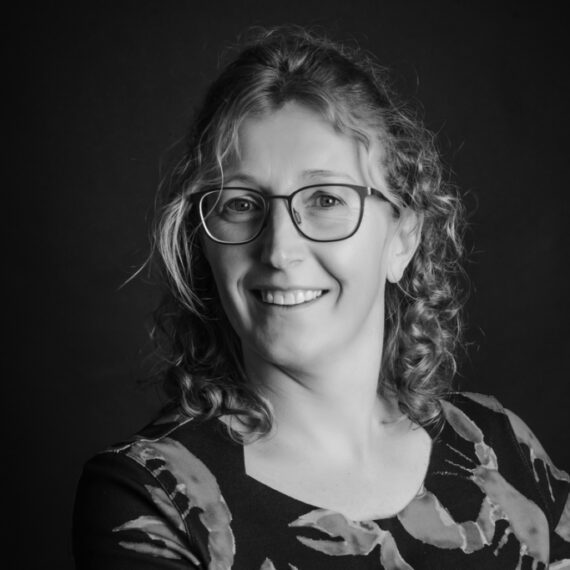
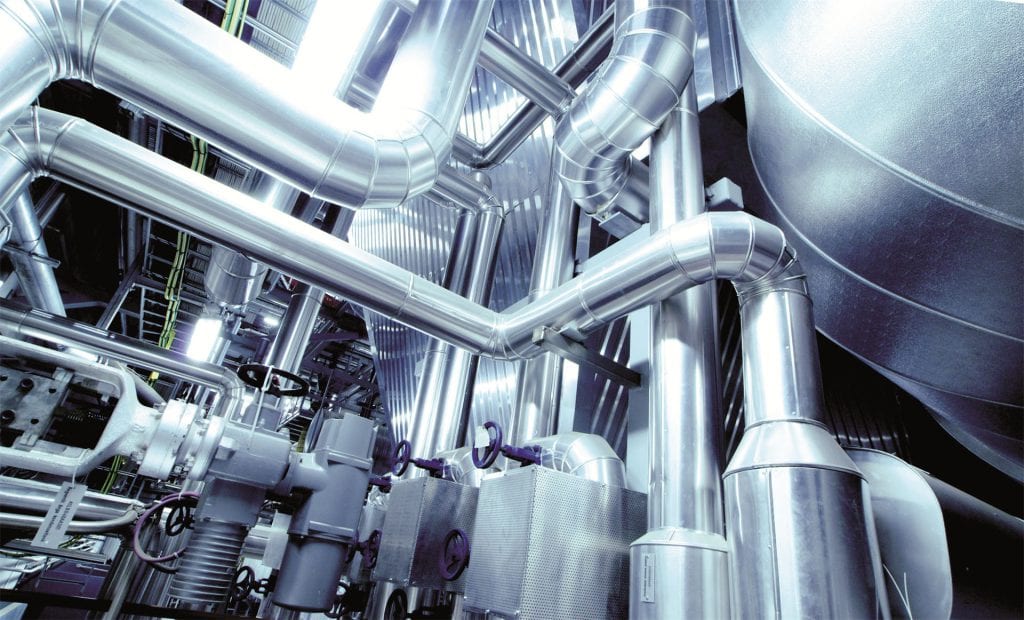